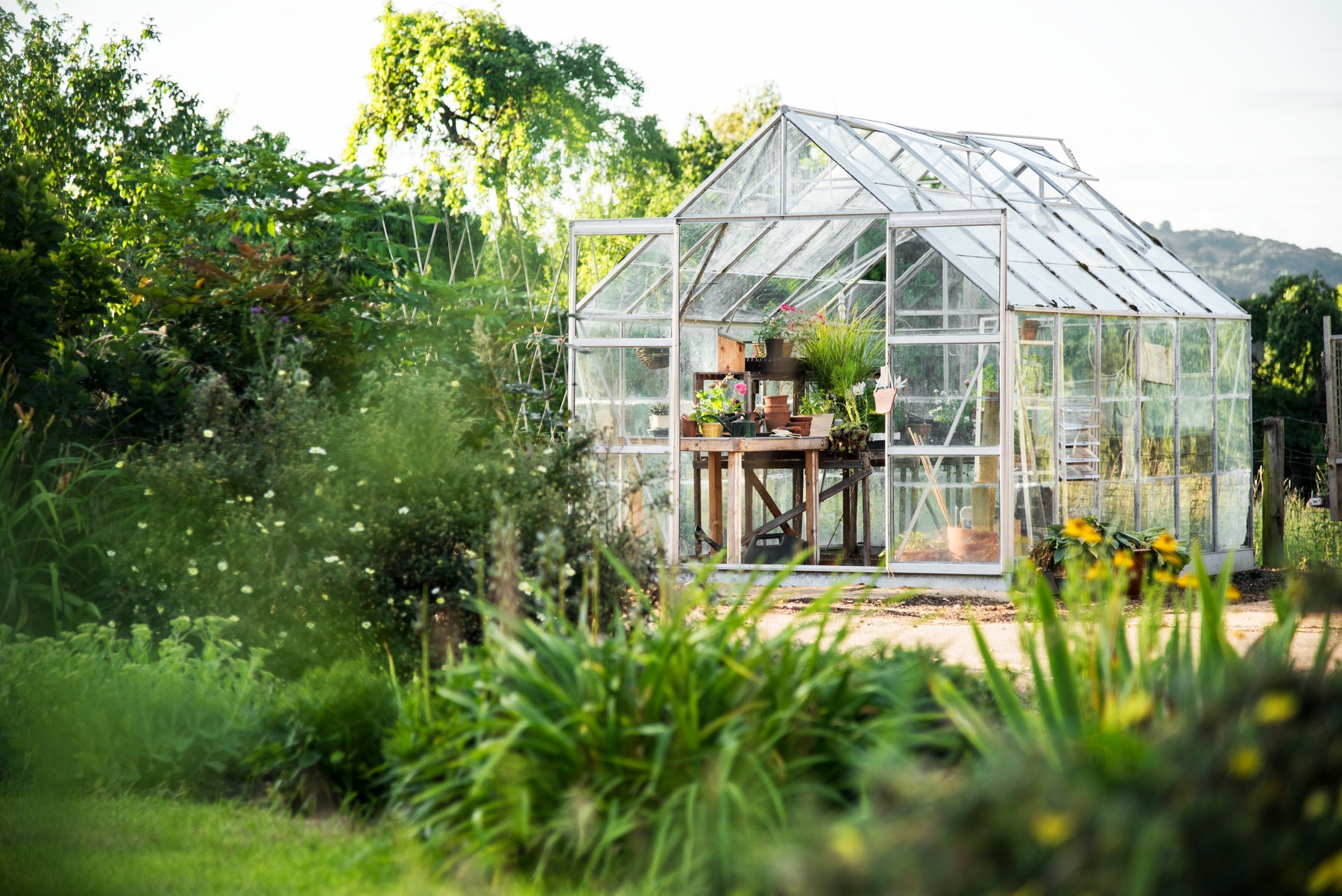
Difference Between Cast and Extruded Acrylic
Cast acrylic and extruded acrylic are both produced from the same base thermoplastic; PMMA; Polymethyl Methacrylate, more commonly known as “perspex” or “plexiglass”. The different production processes are responsible for their slightly different properties and result in them being suitable for different applications.
CAST ACRYLIC
Cast Acrylic is formed by pouring molten PMMA monomer resin into a mould. The mould consists of two large glass sheets, and the desired thickness of cast acrylic sheet is achieved by the distance of separation left between the glass sheets. The void between the glass sheets is then filled with molten PMMA. This production process does mean that there can be up to a 20% tolerance difference of thickness throughout the sheet; i.e., a 5mm sheet produced may be 4mm in places etc.
There are two techniques to complete the polymerisation of the PMMA, leaving you with a solid sheet of cast acrylic. The mould is either submerged in warm water or baked in an oven.
The casting of PMMA results in a much more closed molecular structure. This results in the sheets being stronger and having better chemical and scratch resistance than extruded acrylic. It is suitable for laser cutting, leaving you with polished edges, cutting shapes on a CNC router, diamond polishing of edges, and laser engraving.
The production process of cast acrylic lends itself to the opportunity to add colour to the clear PMMA monomer resin, resulting in the availability of a more extensive range of colours.



Cast acrylic applications:
- Building and Construction
- Art installations
- Retail shop fitting
- POS Displays
- Signage/lightboxes
- Sneezeguards
- Machine guards
- Noise barriers
- Trade show/exhibition stands




EXTRUDED ACRYLIC
Extruded acrylic is formed by passing the molten PMMA monomer resin through an extrusion line die. This extruder compiles of a feeder/hopper; which the PMMA is fed into, a solid base, and a series of steel rollers/dies, which the molten PMMA passes under and above; not dissimilar to the rolling of pastry. The desired thickness of the sheet is achieved through the distance left between the base and the final roller/die that the molten mass passes under. The resulting continuous length of extruded PMMA is then cut at the desired length of extruded acrylic sheet. The extrusion process gives you a much more accurate final sheet thickness than cast acrylic, with a 5% - 10% sheet thickness tolerance achieved; ie: a 5mm sheet can be 4.5mm – 4.75mm.
The extrusion process of PMMA sheets results in a much more open or stretched molecular structure and grain direction. This process means that extruded acrylic has a lower chemical resistance and is slightly less scratch resistant than cast acrylic. It also may not lay as flat as cast.
Like cast acrylic, extruded acrylic can also be laser cut with great results, leaving you with polished edges. It is more suitable than cast acrylic for flame polishing of edges but less suitable for diamond polishing. It can also be machined on a CNC router.
Extruded acrylic sheet is also more suitable for thermoforming of shapes and hot line bending.
When it comes to colour options, whilst it is possible to produce extruded acrylic colours, it is a more laboursome process than cast acrylic. Therefore, there is a less extensive range of colours available.
Extruded Acrylic applications:
- Greenhouses
- Leaflet holders
- Retail display
- Glazing
- Architectural model display cases
- Roof lights and domes
- Picture framing
- Signage
- POS Displays
- Sneezeguards



Cast Acrylic and Extruded Acrylic Compared
Features | Cast Acrylic | Extruded Acrylic |
---|---|---|
COST | More expensive than extruded as the process is more labour intensive | Process makes it more cost-effective |
THICKNESS | Larger range of thicknesses available | Formed in a single sheet and limited to thinner sheets |
STRENGTH | Much harder and more robust than extruded, high impact resistance | Softer, not as impact resistance |
CUTTING | Can be cut to any shape | Better for straight cuts |
INSTALLATION | Great for smaller projects and large fabrications relying on durability | Ideal for large projects |
HEAT BENDING | Harder to bend and shape as it has a higher melting point | Easy to bend as has a lower melting point |
LASER ENGRAVING | Produces a frosty look with polished edge that won’t bend or chip during cutting | Produces fumes, prone to stress cracks |
FLAME POLISHING | Harder to flame polish | Easy to flame polish |
SCRATCH RESISTANCE | More scratch resistance | Less scratch resistance |
CHEMICAL RESISTANCE | More chemical resistant | Less chemical resistant |